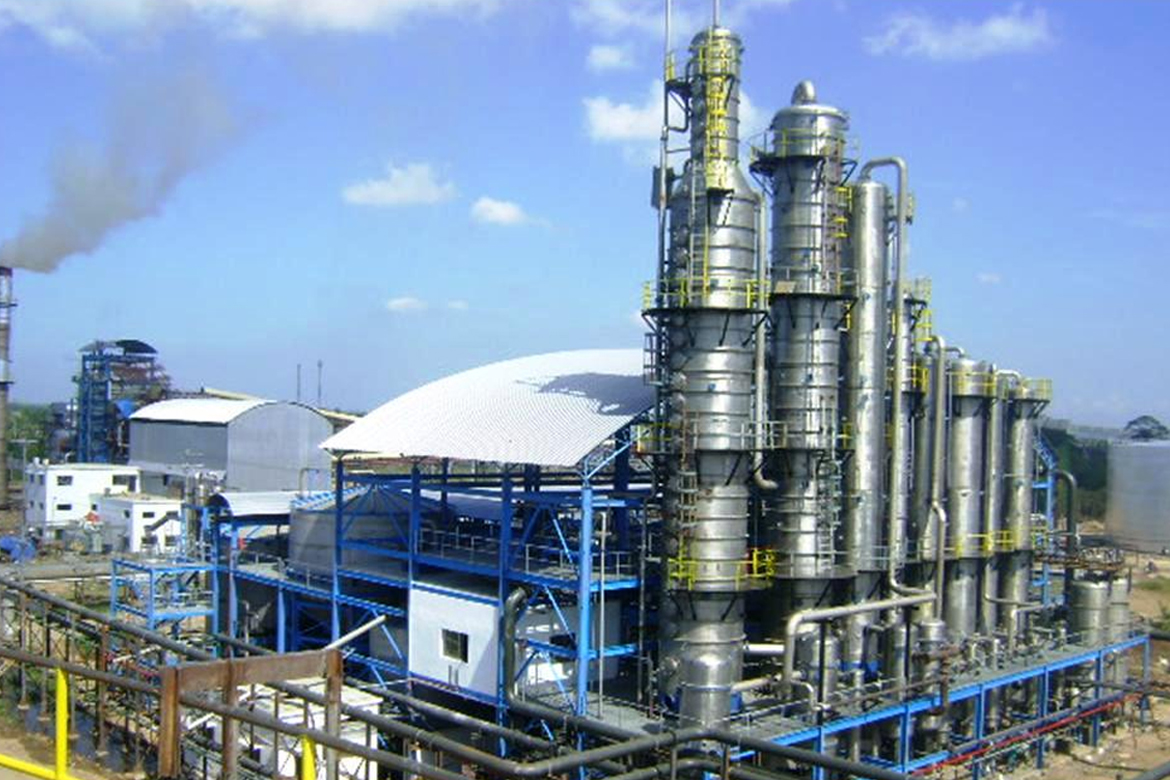
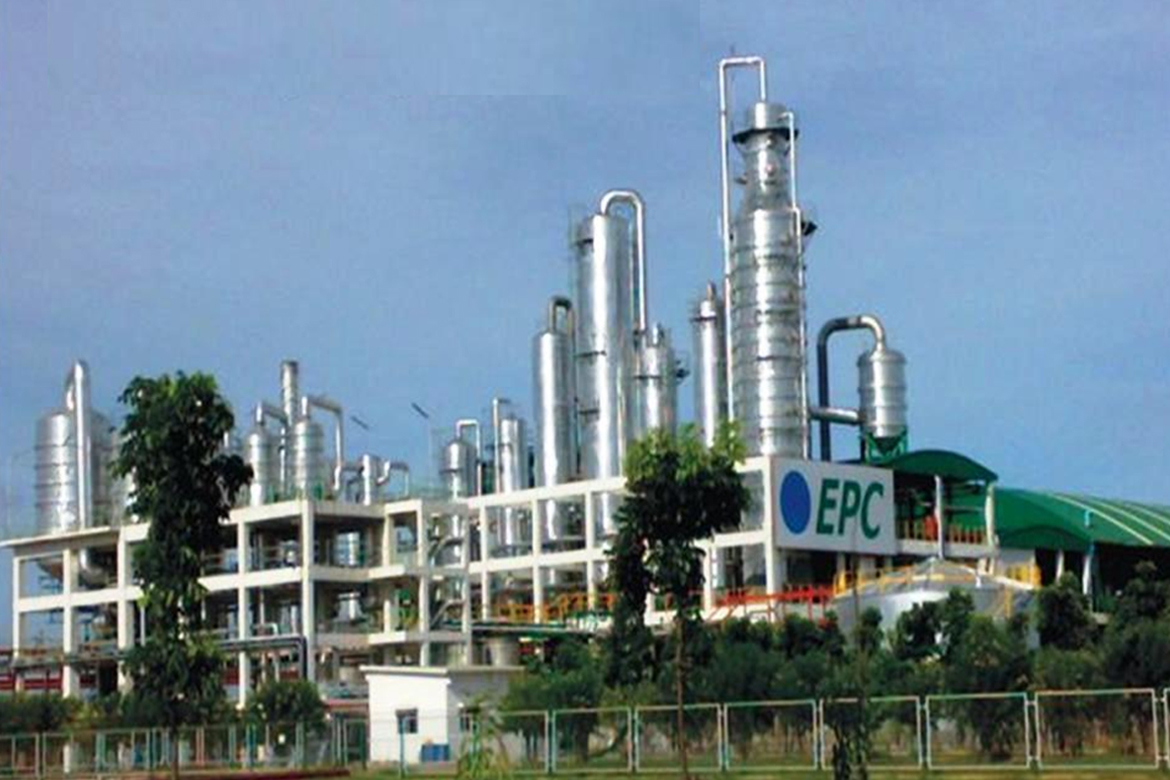
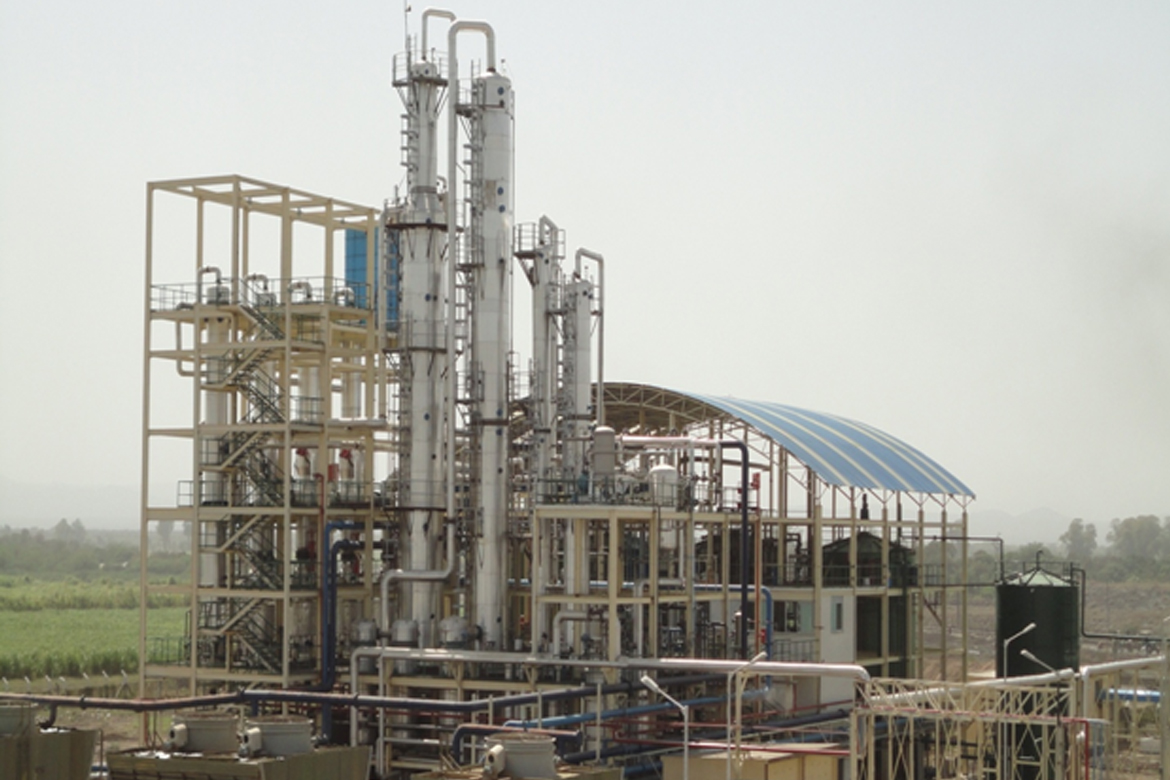
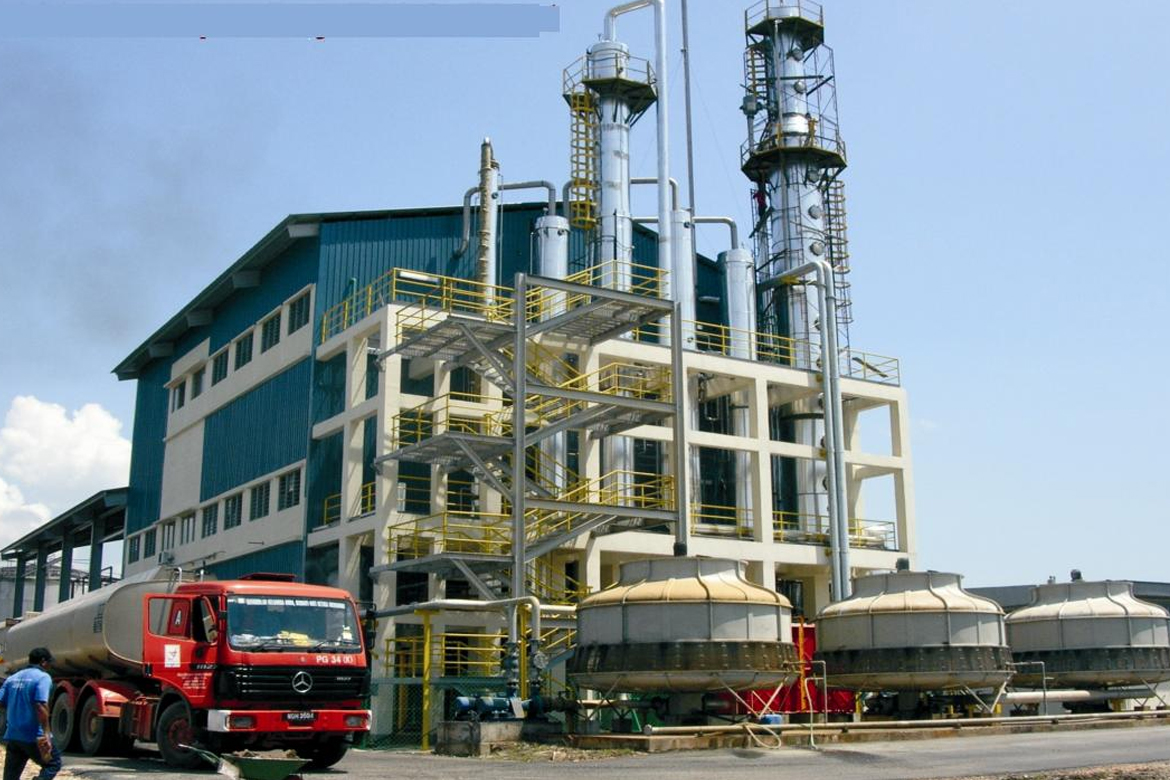
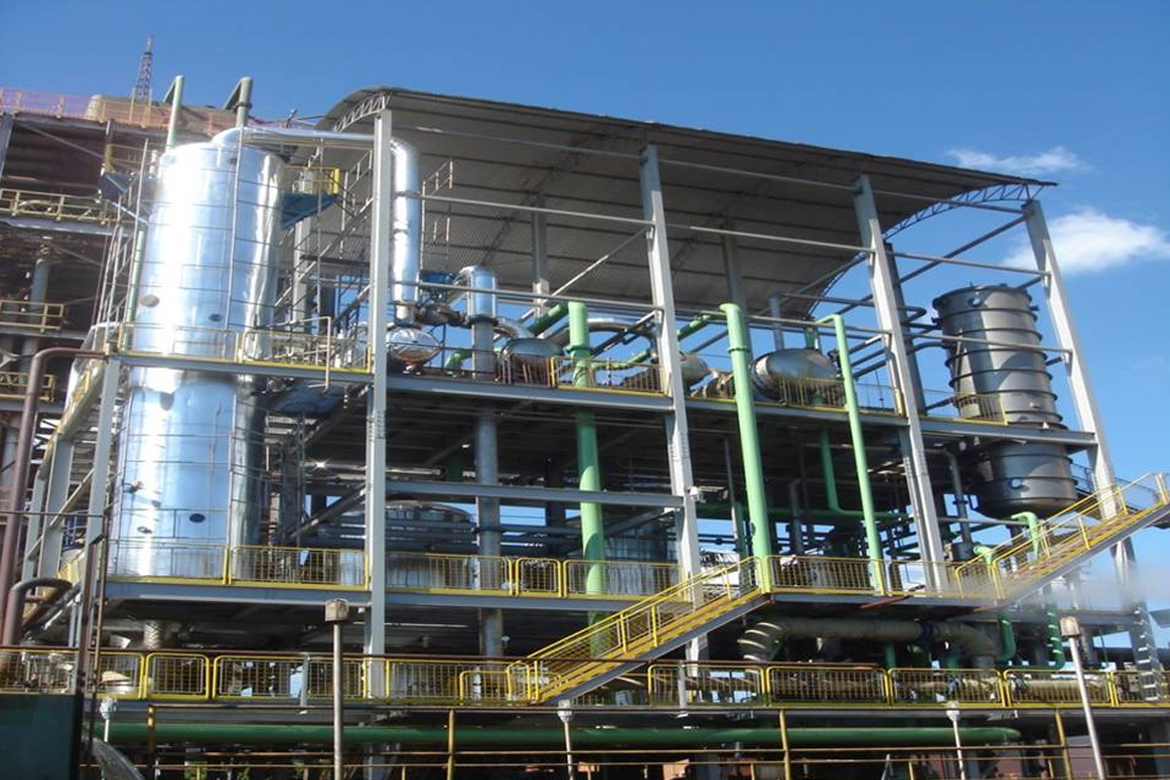
"K-SUPER" MULTI PRESSURE DISTILLATION
In the earlier days Atmospheric distillation technology was used to separate alcohol from Fermented wash, which had certain disadvantages like higher steam consumption, poor quality of Alcohol& scaling of distillation columns due to high temperature operation. However after development of Multi Pressure vacuum distillation technology, all distillation plants are designed on this technology.
The multi pressure distillation has many advantages over conventional atmospheric distillation plants like lower energy requirement, very good quality alcohol and less scaling of the distillation trays due to sludge. The vacuum distillation produces ethanol of international quality standards and there is a lot of demand of ethanol from the vacuum distillation process.
“The Extra Neutral Alcohol produced from this latest technology will meet most of the international quality standards for ethanol like US Pharmacopoeia, British Pharmacopoeia and Japanese standards”.
The vacuum distillation approximately requires 50% less steam as compared with the conventional old distillation technologies. The vacuum distillation consists of distillation columns with high efficiency column trays, condensers, reboilers, vacuum pumps and reflux pumps. A closed loop cooling tower system with an induced draft-cooling tower with circulation pumps is also provided to ensure higher cooling efficiency and to minimise water wastage.
In this vacuum distillation alcohol is separated and concentrated using principal of fractional distillation. This is based on difference in boiling points of volatile compounds in the mixture. There are eight distillation columns in the system Primary column also called Mash column, Degasser column, Pre-Rectifier column, Hydro extractive distillation column, Final Rectifier column, Refining column, Dealdehyde Column and Defusel Column
The Primary or Mash column is operated under
vacuum and it is heated using the vapours from the Rectifier column, which is
operated under a slightly higher pressure. The vacuum operation of the Primary
column will help in reducing the overall energy requirement and also improve the
product quality.
Due to vacuum operation of the Primary column the scaling of the column trays is
minimised and plant can be operated without stoppage for a longer duration as
compared with atmospheric plant.
The fermented mash is preheated using a beer
heater at the top of the Primary column and followed by a plate heat exchanger and
finally delivered to the top of Primary column. The pre heating of mash in two
stages recovers energy and saves steam required for the distillation. The mash runs
down the Primary column from tray to tray, while vapour goes up in the column
contacting the mash at each tray.
As a result of this contact and boiling, alcohol and other impurities along with
some water are stripped in the form of vapours and remaining mash in the form of
vinasse (effluent) is disposed off from the bottom of the Primary column for ETP.
When the vapours of alcohol and other volatile
compounds reach the top, they are separated out from the top of Primary column and
taken to PreRectifier column where they are condensed in beer heater and other
Primary condensers.
The heat is supplied by the Final Rectifier vapours from the Reboilers provided
at the bottom of the Primary column.
Two reboilers are provided at the bottom of the Primary column to facilitate the heat transfer from Rectifier column to Primary column. The vapours from Pre Rectifier column top condensed in the above condensers are collected and then sent as reflux liquid. The RS drawn from this column and is fed to RS cooler and sent to RS Storage section Via Safe & Tester Assembly.
The RS is fed to the Hydro extractive distillation column for purification. The ethanol streams from other columns are also diluted with soft water and are fed to Hydro extractive distillation column via a feed preheater (plate heat exchanger). A Reboiler is installed at the bottom of the Hydro extractive distillation column. Impurities such as Aldehydes and Fusel oil are removed from the top of the Hydro extractive distillation column and are fed to Fusel oil concentration column, while dilute ethanol along with fewer impurities, are taken from the bottom of the Hydro extractive distillation column and fed to Rectifier column middle. Steam is fed to Hydro extractive distillation column through Reboiler.
A Reboiler is installed at the bottom of the Rectifier column, which heats the process liquid i.e. alcohol and water received from the Hydro extractive distillation column, indirectly with the help of steam. In the Rectifier column, the ethanol is concentrated to 96 % by refluxing the Rectifier reflux liquid. Extra neutral ethanol (ENA) is tapped from the top of Rectifier column, which is directly sent to Refining column for removal of other low boiling impurities. While the bottom product of the Rectifier column called spent lees is drained off. The higher alcohols also called light and heavy fusel oils are removed from the middle portion of the Rectifier column so that they are not mixed with Extra Neutral Alcohol.
Light and Heavy fusel oil from Rectifier column
and top cut from Hydro extractive distillation column plus ester cut from Hydro
extractive distillation column is fed to Fusel oil concentration column.
The steam is delivered from the bottom of the Defusel Column to allow the desired
separation. Fusel oil consisting of higher alcohols viz. amyl alcohol, iso amyl
alcohol, n-propanol etc. are concentrated near middle portion of Fusel oil
concentration column and can be removed and separated in the Fusel Oil Decanter in
sufficient higher concentration. While the bottom product called spent lees is
drained off.
The top product from the Defusel Column is
cooled in the cooler and sent to storage as Technical Alcohol.
The Refining column is fed with the ENA from the Rectifier column, which is boiled
off in the Refining column to remove the low boiling impurities like methanol and
mercaptants.
Extra Neutral Alcohol (ENA) is tapped from the bottom of the Refining column, which
is cooled upto 30 oC, by passing through ENA cooler.
The impure ethanol, which contains many
impurities, is drawn from the top of the Refining column and cooled in the cooler
and sent to storage as Technical Alcohol. Alternatively diluting with soft water in
Dealdehyde Column as and when required can further purify some of these Technical
Alcohol streams.
Both fermentation and distillation are operated with DCS controls system. This will
help in maintaining the parameters consistent and without any fluctuations. Most
modern distillery plants use computer system for controlling their parameters.
Advantages of "K-Super" Distillation Process
- Overall Scheme
- Vacuum operation (low temperature) of Analyzer / Mash column ensures minimum scale formation of the trays / other column internals and hence very low cleaning frequency of Analyzer / Mash column is required. This avoids frequent shutdown of plants for maintenance.
- Thermosiphon reboilers are used for distillation columns. Hence no need of recirculation pumps. Therefore less electricity consumption for Distillation plant operation
- Use of simple water ring vacuum pump instead of water jet ejector. Hence there is saving of fresh water in the process.
- Provision of Sealing water systems for Vacuum Pumps & all process pumps mechanical seals result into substantial saving of Soft water in the Operation.
- Multipressure Vacuum Distillation
- Multipressure operation results in to good overall energy savings over a longer period.
- Vacuum operation (low temperature) of Mash column ensures minimum scale formation of the trays / other column internals and hence very low cleaning frequency of Mash column is required.
- Lower temperature operation causes less pyrolysis in Mash column hence we ensure good quality alcohol.
- Much better stripping (separation) of low boiling impurities takes place under vacuum conditions.
- Less steam consumption for distillation column due to Vacuum operation of Analyzer/ Mash column.
- Simple ENA
distillation scheme
- The distillation scheme consists of optimum number of distillation columns and their configurations, allowing lower capital cost.
- The scheme of distillation is very simple and allows easy operation.
- The simple distillation scheme allows for a cost effective level of automation using DCS system.
- The overall electricity requirement is also low, as compared to other complicated multipressure distillations.
- Effective separation
of Impurities and alcohol quality
- Better quality ENA, as both low boiling and higher boiling impurities are separated effectively in dedicated columns.
- Vacuum conditions also help in separation of many impurities.
- The alcohol produced is of Neutral taste and character, with a Potassium Permanganate Test Time of around 50 to 60 minutes as BP 1993 method.
- The number of trays and tray spacing in each column are designed, for handling different quality of fermented wash.
- The same distillation scheme can be easily made flexible to produce different quality products depending on the requirement.
- Higher Distillation
efficiencies
- The distillation trays are of Bubble Cap construction, designed using vast experience, resulting in to good tray efficiencies at varying conditions.
- The turndown of the distillation plant is as high as 40 to 50%, which allows the operation at 40 to 50% capacity, without any significant change in the efficiency and steam consumption.
- Mash column losses are quite low due to less scaling at lower temperature operation.
- The alcohol vapors, after vacuum system are scrubbed to recover maximum alcohol.
- Instrument System
using DCS (Distributed Control System)
- DCS system is a most cost effective instrumentation system for distilling industry.
- It results in to a very high consistency level in terms of alcohol quality, distillation efficiency and energy consumption.
- The distillation operation requires less manpower.
- The DCS system allows easily changing the operating parameters to produce different quality alcohol as and when required.