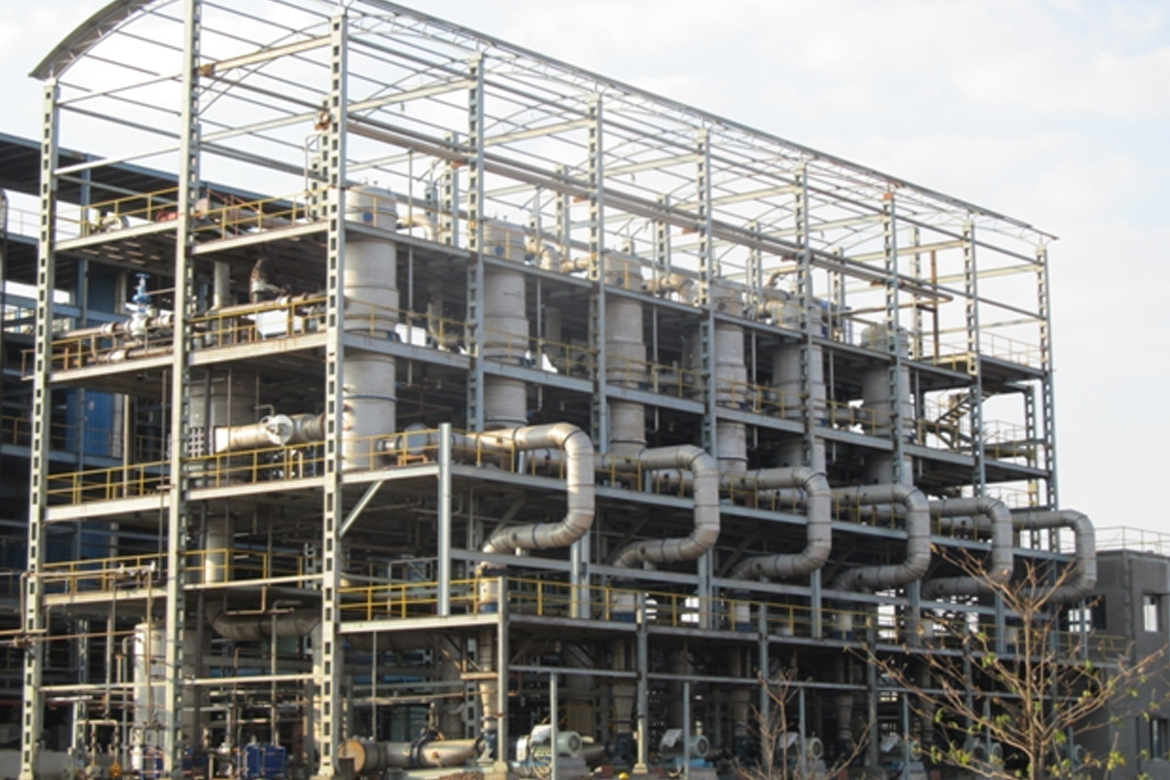
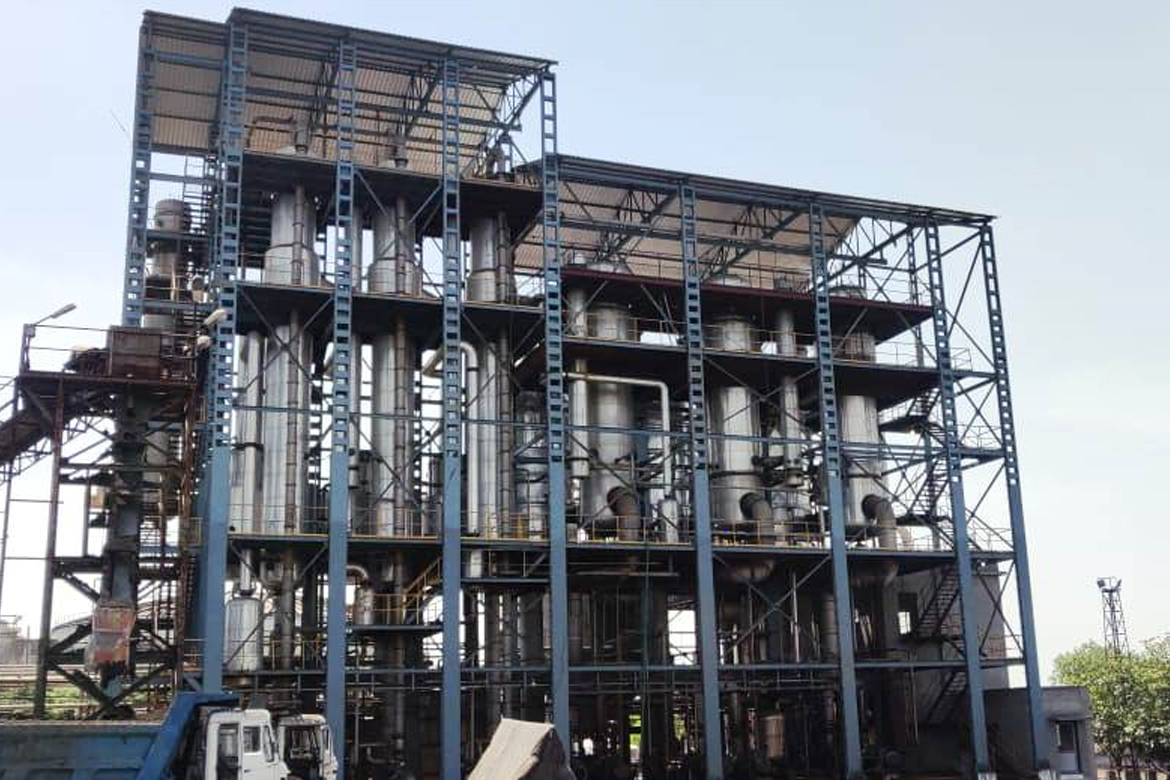
"K-Super" EVAPORATION is an operation used to remove a liquid from a solution, suspension, or emulsion by boiling off some of the liquid. It is thus a thermal separation, or thermal concentration, process. We define the evaporation process as one that starts with a liquid product and ends up with a more concentrated liquid as the main product from the process.KBK offers Evaporation plants with various combinations of Falling Film and Forced Circulation Evaporators.
Based on Process requirement, Evaporation Plants are designed as per the following schemes:
-
INTEGRATED EVAPORATORS (STAGE I)
-
STANDALONE EVAPORATORS (STAGE II)
"K-Super" Integrated Evaporator
"K - SUPER" INTEGRATED EVAPORATION plant is designed with Three/four effect Falling Film Evaporators.In falling film evaporators, liquid and vapors flow downwards in parallel flow. An even thin film enters the heating tubes via a distribution device in the head of the evaporator, flows downward at boiling temperature, and is partially evaporated. This gravity-induced downward movement is increasingly augmented by the co-current vapour flow.
In "K – SUPER" INTEGRATED EVAPORATION, first evaporator get heat from the vapour of Analyzer Column @72 to 73 ºC temperature. Spent wash
vaporised in first stage give energy to second stage. There is no need of any steam
in this stage. Vapour condensed in first stage send back to Dealdehyde column as
reflux. There are total five falling film evaporator in first stage. Evaporators are
in forward feed arrangement. Vapors of Second evaporator are fed to third effect Evaporator.Vapours of third effect evaporator get condensed in a surface condenser. The condensate is collected in a tank and transferred to Condensate polishing unit for further treatment. Falling film evaporators can be operated at very low temperature
differences between the heating media and the boiling liquid, and they also have
very short product contact times, typically just a few seconds per pass.
These
characteristics make the falling film evaporator particularly suitable for spent
wash evaporation.
In "K – SUPER" INTEGRATED EVAPORATION, there is specifically
designed Spent wash distributors for the proper distribution of Spent wash in
tubes.
Specific design of the liquid distribution system achieve full and even product
wetting of the tubes. Because of the low liquid holding volume in this type of unit,
the falling film vaporator can be started up quickly and changed to cleaning mode
easily.
In "K – SUPER" INTEGRATED EVAPORATION Falling film evaporators are highly responsive to alterations of parameters such as energy supply, vacuum, feed rate, concentrations, etc. it will be equipped with a well designed automatic control system therefore it can produce a very consistent concentrated product.
"K-Super" Standalone Evaporator
In "K – SUPER" STANDALONE EVAPORATION, second stage consists of four or five effects with either combination of Falling Film & Forced circulation evaporators or only Forced circulation evaporators.. First effect evaporatoris driven by Steam at suitable temperature or process stream @ 1 Kg/Cm2 pressure and 95-100 ºC temperature. Evaporators are in forward feed or Backward feed or Mixed feed arrangement. The second effect will be driven through the vapors from the first effect. The third effect will be driven through the vapours from the second effect and so on. vapours from the last effect are condensed by the surface condenser and send for further treatment. As per requirement, first effect is provided with stand-by unit and CIP. Also floating arrangement of evaporators are made so that any of the effect can be taken for cleaning without stoppage of plant operation.
In "K – SUPER" EVAPORATION, Forced circulation evaporator are designed in such way that the flow velocity in the tubes is high, which prevent the choking of the tubes. All the process condensates arecollected in a tank and send to condensate polishing section. Final concentrated Spent wash comes out from first/last effect and it is send to boiler for incineration.
Advantages of "K-Super" Evaporation
- Evaporation plant can be designed for either Raw Spent wash or Bio-methanated spent wash or Combination of both.
- Proper selection of Materials of construction for different components of Evaporators based on feed characteristics of Spent wash.
- Evaporation plant is fully operated through PLC & SCADA, manual intervention is voided & therefore consistent operating parameters are achieved.
- Plant capacities are achieved as per the agreed Performance parameters over a longer period.
- Evaporation plants are designed with 15 to 20% margins, so that any fluctuations in plant capacities can be taken care.
- For concentration of spent wash up to 30 to 60% in case of Molasses based or 30 to 35%in case of Grain based plants,Specific steam consumption is very less.
- Provision of Stand by pumps, Stand by body and CIP system ensures uninterrupted plant operation for a longer period, which results in saving of chemicals, consumables and manhours. Therefore reduction in operating cost is achieved without any additional investment.
- As the Integrated Evaporators are falling Film Evaporators, recirculation pumps capacities are less as compared to Forced circulation evaporators recirculation pumps. Hence less electricity consumption for Integrated Evaporation plant.
- Vacuum operation (low temperature) operation of Evaporator bodies, ensures minimum scale formation of the tubes and hence very low cleaning frequency of Evaporators.
- Substantial saving due to less down time over a longer period.
"K-Super" DECANTATION & STILLAGE HANDLING SECTION:-
The stillage from Distillation section is fed to Decanter centrifuge. Depending upon Plant capacities quantity of Decanter centrifuge are considered. Apart form no. of working Decanter Centrifuge one no. is kept as Stand-by. In the Wet cake with 28-30% w/w solids is removed from the bottom of Decanter which can be sold directly as cattle feed (DWGS).The thin stillage separated from the Decanter is collected in a collection tank. Part of the stillage is recycled back to Liquefaction section and remaining is taken to Flash tank at the bottom of Analyser column. From flash tank thin stillage is circulated through Reboilers installed at the bottom of Analyser column. Energy to Reboiler is provided with the help of top alcohol vapor from Rectifier column. The partially concentrated stillage from flash tank is taken to Evaporation plant for concentration up to 30-35% w/w solids.
"K-Super" DDGS Dryer
DDGS (Dry Distillers Grain Solubles) is the by-product of Grain based Distillery which is the revenue generation product apart from main product. Grain based distilleries feasibility depends on efficient recovery of DDGS product.
Wet Cake mixed with concentrated Syrup from Evaporation plant in Paddle Mixer. The Paddle Mixer also receives part of dried material re-cycled from system. The wet cake is pre-conditioned with the above in Paddle Mixer before feeding into the Dryer. Discharge from Paddle Mixer is then admitted into the Screw Feeder, which in turn feeds the material into the Dryer. The Tube Bundle Dryer comprises of rotating Tube Bundle housed in a stationary housing. The steam is admitted into the tubes through Rotary joint from one end of the Tube Bundle and the condensate is collected out from the Tube Bundle through Rotary joint and suitable siphon arrangement from other end of the Tube Bundle.
The Tube Bundle is provided with suitable flights mounted in the spiral fashion on the periphery for effective showering of the material on to the tubes and then transferring heat & drying of the material. On the discharge port of the dryer, a suitable manually adjustable weir is provided to adjust the material residence time in the dryer. Dried material is discharged through outlet discharge port through extraction screw. Extraction Screw discharges the material into Dryer Recycle System & dried material is discharged from this system.
Ambient air is sucked from the openings provided on the housing. Vapours formed in the dryer are sucked by vapour fan & exhausted to atmosphere through a cyclone separator. Cyclone separator is provided with steam tracing to minimize condensation on the inside surfaces.
Advantages of "K-Super" DDGS Dryer
- DDGS Dryer is designed on various type of raw materials.
- Proper selection of Materials of construction for different components of DDGS Dryer based on characteristics of DWGS.
- Performance of DDGS Dryer achieved as per the agreed Performance parameters over a longer period.
- DDGS Dryer is designed with 15 to 20% margins.
- Trouble free operation of plant with less down time & low maintenance cost
- DDGS Dryer vapor is integrated with Standalone Evaporation plant, hence there is no need of additional Steam for Evaporation plant operation. Therefore there is substantial reduction in operating Cost.
- DDGS Dryer is provided with Cooling, Conveying, Storage system along with Bagging and sealing equipment.
- Excellent quality of DDGS product with maximum 10% moisture is achieved.