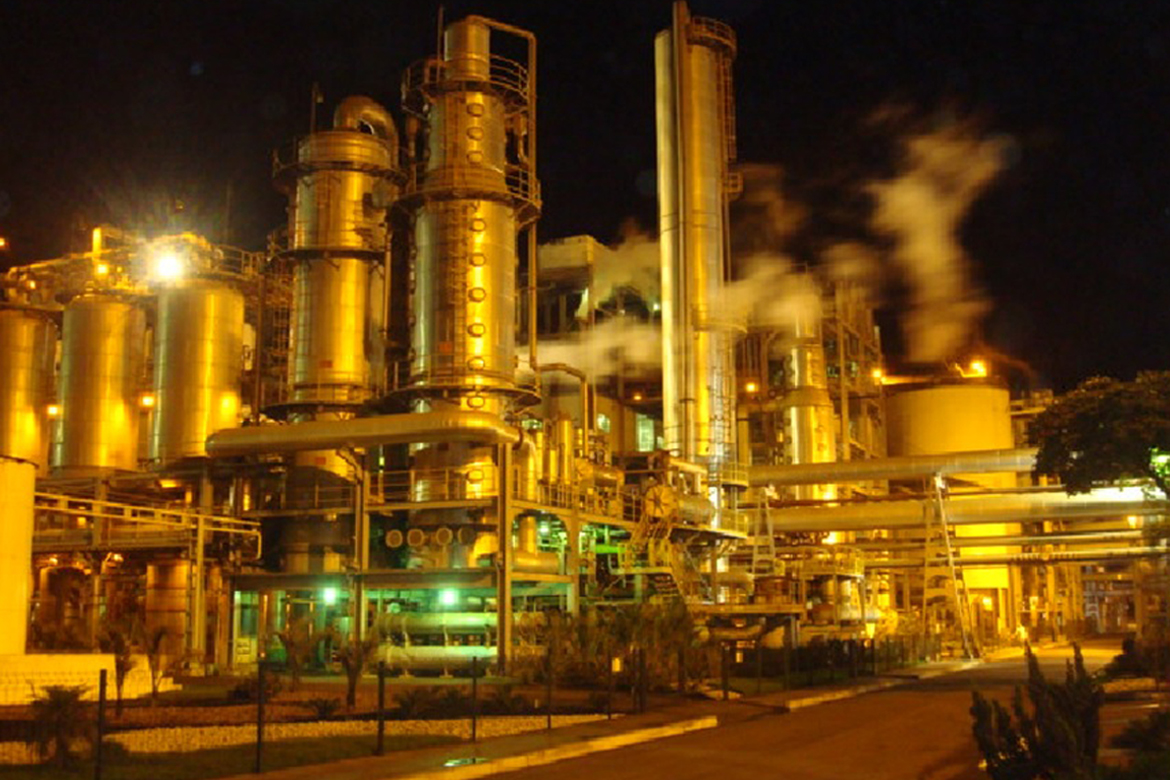
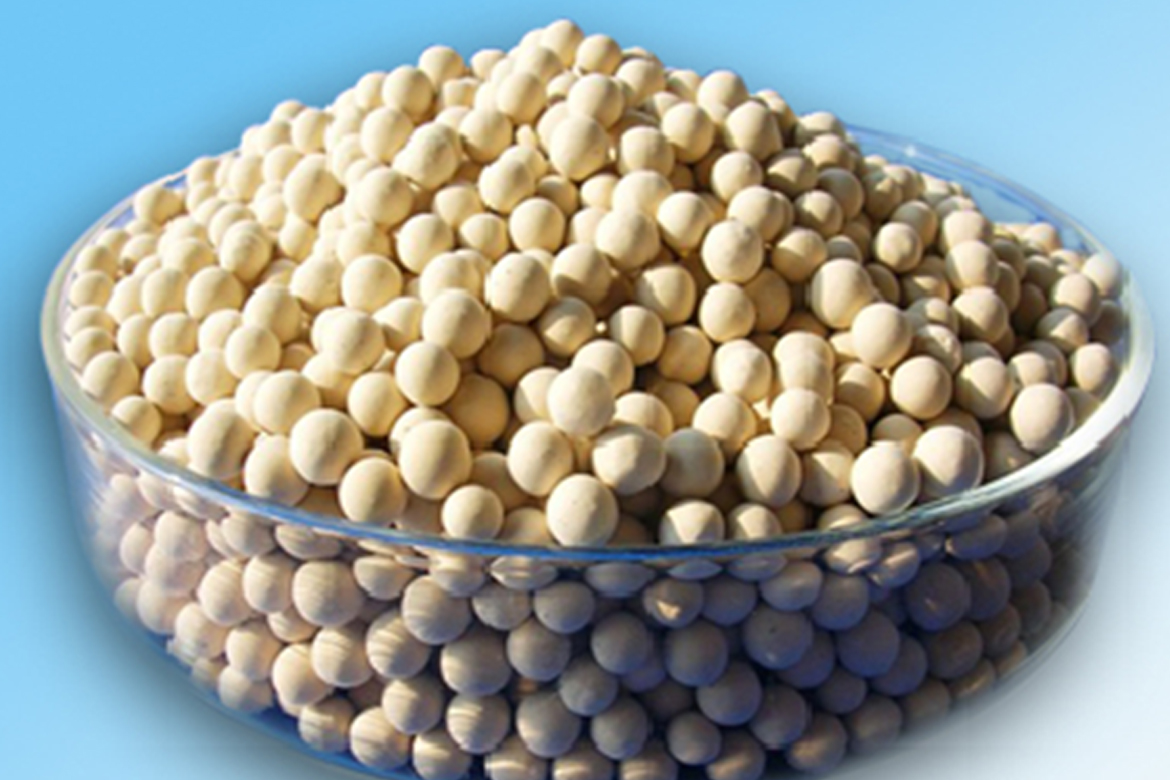
K-SUPER Ethanol
Molecular sieve technology works on the principle of pressure swing adsorption. Here water is removed by adsorbing on surface of ‘molecular sieves’ and then cyclically removing it under different conditions (steaming).
Molecular sieves are nothing but synthetic zeolites typically 3A zeolite. Zeolites are synthetic crystalline aluminosilicates. This material has strong affinity for water. They adsorb water in cold condition and desorb water when heated. This principle is used to dehydrate ethanol. The crystalline structure of zeolites is complex and gives this material the ability to adsorb or reject material based on molecular sizes. Water molecule can enter the sieve and be adsorbed, but larger alcohol molecule will not be retained and will go through the bed. There can be two to three beds in parallel. Once a particular bed is saturated with water, it is heated with steam so that adsorbed water is desorbed from the bed. Till that time, other bed is used for dehydration.
This type of system is characterized by high capital investment. Low steam consumption and low power consumption as compared to distillation. The only disadvantage of molecular sieves is the high attrition rates of sieves in case of small plants. Hence, typically, some amount of sieve material needs replacement periodically, thereby resulting in higher cost of production in case of small capacity plants. In case of large capacity plants, the molecular sieve is the most optimum both in terms of initial investment and operating cost. The total unit is operated with DCS computer controls system. This will help in maintaining the parameters consistent and without any fluctuations. This is the common method used in modern distillery plants for controlling their parameters.